刀具的使用
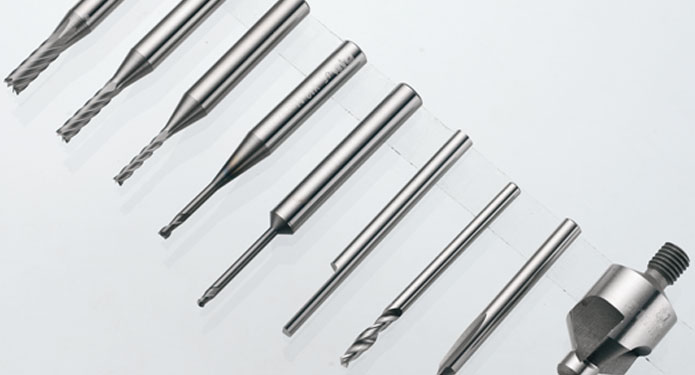
不管刀具設計得如何,或用什麼材料製成,刀具的製造商都應該提供切削速度和每齒進給量的初始值。如果沒有這些資料,就應該向製造廠家的技術部門諮詢。廠商 應該熟知他們的產品在進行全寬度開槽銑削、外廓銑削、插銑或斜坡銑削時的能力如何,因為許多標準銑刀大多數不能完成這樣多的加工工序。比如,如果銑刀沒有 足夠大的第二後角,則斜坡銑削的斜角就要減小。
很明顯,如果超出刀具的加工能力,將導致刀具的損壞。插銑也是一樣,如果不能將切屑及時地從槽底排出,切屑將會受到擠壓,之後刀具也將損壞。總之,銑削加工高溫合金時,這些情況對刀具壽命都是不利的。
如果認為減慢進給速度可延長刀具壽命,事實證明是錯誤的。典型的例子就是在切第一刀時,會發現材料相當硬。如果把進給量減小 ( 如可轉位銑刀的每齒進給量減至 0.025~0.5 mm ) ,刀具切削刃將強烈地摩擦工件,結果是刀具很快或是立即損壞。摩擦能引起工件表面的加工硬化,為避免加工硬化,切第一刀時應保持一定的切削負荷 ( 0.15~0.2 mm/ 每齒進給量 )。
切削深度取決於多種因素,如刀具設計,刀片高度、刀具剛性、刀具總長、機床馬力等。但當刀具的後角和前角為 5°~11° 正值時,最適於加工粘度大的材料。立銑刀的螺旋角應該在 35°~50° 之間。這些銑刀的傾斜刀刃有鋸削作用,能形成理想的切屑並帶走切削熱。
當然,難切削材質時,適當的切削速度也非常重要。它決定了在切削區產生熱量的多少。推薦的速度範圍從較低的 12~15 m/min ( 對高速鋼銑刀 ) 到 23~37 m/min ( 對硬質合金銑刀 ),再到180~245 m/min 或更高( 對陶瓷銑刀 )。增加進給量和切削深度也會增加切削熱,因相應地增加了切削力和刀具與工件的接觸面積。
根據銑削難切削材質時的應力和切削力,應選擇由K40~K50硬質合金作為銑刀刀片的基體,並採用帶有耐熱性能高的氮鋁鈦塗層。使用這類硬質合金牌號的刀片進行銑削 加工,可取得很好的加工效果。在較低的切削速度下,採用碳氮化鈦塗層進行加工,其效果也不錯。
如果在加工中,刀具使用不當,即使用最好的基體和塗層,也不會取得好的加工效果。比如,在零件上要銑出一個深度為 2~5mm 的槽,想分三次走刀加工出來。一般在這個加工過程中 CAM 系統將顯示為三次切深都一樣。由於工件重複地接觸刀具上同一部位,最終相同的切深將使塗層上產生一個缺口,一旦這個缺口劃穿了塗層,就會損傷基體,致使刀 具損壞。
因此在銑削加工中,選取適當的切削深度 ( 一般在 0.5~0.60mm ) ,在銑削時,防止工件重複接觸刀片同一部位,這樣才能延長刀具的壽命。
最新消息
- CNC刀片如何應用評估
- cnc切削刀具價格如何判定?
- 蜂巢式玻璃纖維複合材料
- 刀具選擇基本條件
- 銑刀加工常見問題
- 立銑刀的再研磨
- 金屬材料介紹
- 類鑽碳膜(DLC)介紹
- 克維拉kevlar介紹
- 瀝青路面介紹
- 乳化瀝青應用
- 乳化瀝青製造介紹
- 乳化瀝青介紹
- 鍛造介紹
- 人造藍寶石製造
- 人造藍寶石介紹
- 拋光加工介紹PART4-化學拋光方式
- 拋光加工介紹PART3-固定磨粒方式
- 拋光加工介紹PART2-游離磨粒方式
- 拋光原理介紹PART1
- 切削加工金屬件表面粗糙度的對應措施
- 切削加工表面粗糙度
- CVD單晶鑽石刀具
- 加工物件與刀具形狀
- 鉸刀介紹-part3-鉸孔
- 孔加工精度
- 加工精度-銑車削
- 硬質合金刀具的焊接作業
- 切削熱的影響
- 刀具的使用
- 刀具在銑削鎳基合金時破損較快?
- 沖壓加工介紹
- 沖壓介紹
- 鋁合金的加工切削特性
- 鋁合金介紹
- 航空材料與加工原則
- 高熵合金
- 鎢鋼材質牌號性能對照表
- 蒙耐爾合金(Monel)
- 吸波材料介紹
- 切削液介紹-切削液的特性及選用
- 切削液介紹-切削液的分類
- 裁切分條圓刀
- 不銹鋼加工
- 不銹鋼標準鋼號對照表
- 不銹鋼專用切削刀具
- 不鏽鋼介紹
- 超精密研磨拋光技術
- 曲軸拋光研磨加工
- 研磨與拋光介紹
- HSS材質對照表
- 擴散粒子 - BW產品
- 鎢鋼圓鋸片切割 - part2
- 鎢鋼圓鋸片切割 - part1
- 如何讓銑刀排屑呈現片狀
- 金屬鏡面加工 - part2
- 金屬鏡面加工 - part1
- 銑床精度與校正 - part2
- 銑床精度與校正 - part1
- 鉸刀介紹 - part2
- 150噸粉末成型機
- 鉸刀介紹-part1
- 纖維增強複合材料切削
- 難切削材質切削加工原則
- 切削顫振
- 波浪槽型銑刀/一般粗銑刀
- 汽車工業應用刀具
- 鎢鋼材質刀具適性與特性
- 切屑形狀及其形成介紹
- 常見切削刀具材料
- 切削刀具製造流程
- 萬用油芯拆裝扳手
- 刀具磨耗與壽命
- 刀具鍍層-超硬薄膜被覆材
- 鎢鋼銑刀逆銑與順銑
- 各材質銑刀切削參考數據
- 奈米核殼粒子SEM簡說
- 端銑刀,鎢鋼端銑刀介紹
- 二氧化矽拋光液應用參數
- 切削刀具材料比較表
- 精密微小切削刀具的製備工藝
- 加工HRC50以上淬火料如何選擇刀具?
- 鈦合金切削加工之特點
- 木工刀具如何選用?
- 刀具材料-高速鋼的知識
- 銑刀的選用 Part-2
- 銑刀的選用 Part-1
- 綠色切削影響刀具技術
- 切削刀具是什麼?
- 精密微小切削刀具的特點
- 銑刀的特色及加工差異
- 各種切削刀具的不同?
- 車床夾爪的夾持長度計算
- 刀具中銑刀的種類及選擇
- 金屬硬材及難切削材定義
- 如何選擇立銑刀加工條件?
- PCD圓鋸片
- 塑化電感機台
- 氧化鋯ZrO2
- 電感全自動生產專用設備
- 90° 階梯鑽頭